Keel Block Innovation using Eslon Neo Lumber FFU:
Trial Adoption Begins at Onomichi Dockyard Co., Ltd. as a Replacement for Natural Wood!
- #Neo Lumber FFU
- #Keel Block Innovation
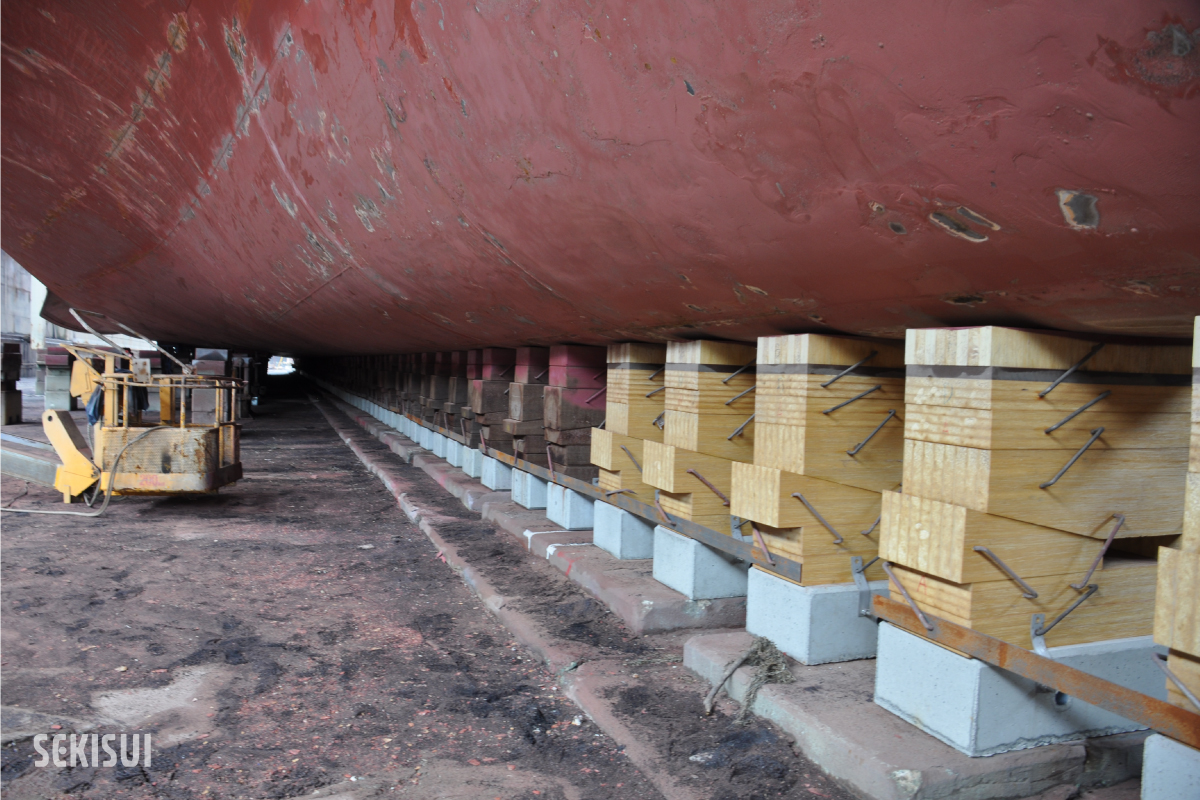
Introduction
In the historic city of Onomichi, Hiroshima Prefecture, a groundbreaking initiative that could revolutionize the global shipbuilding industry is quietly underway. Natural wood keel blocks, indispensable for shipbuilding and repairs, are being replaced with Sekisui Chemical's Eslon Neo Lumber FFU synthetic wood. In this interview, we spoke with Mr. Asami and Mr. Taguchi from Onomichi Dockyard about their decision to trial FFU keel blocks and their impressions of the technology.
Interview : August 8, 2023
Guest
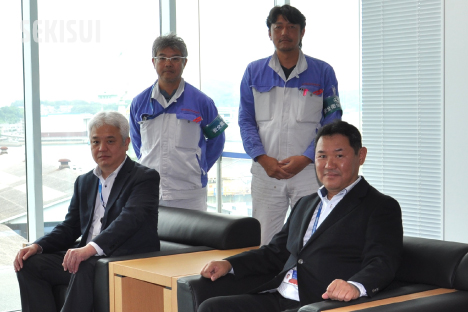
(Front row, from the right)
Executive Vice President & Shipyard Director: Kazuo Murakami;
Managing Director & Deputy Shipyard Director: Kunio Obata
(Back row, from the right)
Shipbuilding Department Manager: Naoto Asami;
Dock Master: Yoshinari Taguchi
Interview
- ———Before discussing FFU, let’s hear from Mr. Naoto Asami, the Head of the Shipbuilding Department at Onomichi Shipbuilding.
-
Mr.Asami : Since its establishment in 1943, Onomichi Shipbuilding Co., Ltd. has built a reputation as one of the few shipyards in Japan specializing in both the construction and repair of ships, with over 80 years of experience. Through the development of our unique ship designs, we have responded to the needs of shipowners by improving cargo capacity, fuel efficiency, and vessel speed. We have built and repaired ships such as product tankers (ranging from 50,000 to 110,000 tons), bulk carriers, and RORO vessels.
As with the introduction of FFU, we are committed to shortening lead times for design, improving processes, and reducing costs. Delivering ships that meet the needs of our shipowners in a timely manner is Onomichi Shipbuilding’s mission.Mr. Naoto Asami, Head of the Shipbuilding Department,
Onomichi Shipbuilding Co., Ltd.
- ———Let’s also hear from Dock Master Mr. Yoshinari Taguchi, regarding the equipment and shipbuilding.
-
Mr. Taguchi : Here we have a shipbuilding slipway approximately 260 meters long, capable of constructing tankers up to 110,000 tons, as well as two dry docks for repairs that can accommodate ships with deadweight tonnages of 60,000 tons and 40,000 tons. Additionally, there are quays for outfitting new ships.
While parts of the ship's bottom and sides that have minimal curvature are being automated at the Ushima Factory, more complex curved sections, such as the stern and bow, which are derived from our unique hull shape, are still finished by hand by skilled craftsmen.
The number of hull blocks assembled on the slipway for semi-tandem operation ranges from 60 to 80. It is also on this slipway that engines, rudders, and propellers are fitted. Some blocks can weigh over 300 tons.Dock Master: Yoshinari
- ———Regarding natural wood keel blocks essential to shipbuilding and FFU from Sekisui Chemical, could you share the background and process that led to the decision to adopt FFU?
- Mr. Asami : Replacing the natural wood keel blocks we have been using with other materials sounds simple, but it is not an easy task. Over the long history of shipbuilding, natural wood keel blocks have accumulated a track record spanning decades, if not centuries, having supported the weight of thousands, even tens of thousands, of tons of ships.
At Onomichi Shipbuilding, we have used tropical hardwood like Apitong for most of our dry dock keel blocks. However, the availability of tropical wood has decreased, and now to find quality materials we have to venture deep into the mountains. Additionally, due to the "wood crisis" the price of timber has risen significantly, and even when purchasing new wood, the quality has declined, with cracks appearing in some pieces.
In short, the time has come when we must find a replacement for the Apitong keel blocks. It’s not something we can start addressing out of nowhere when the need arises. At this point, when I was thinking about possible alternatives, Mr. Taguchi brought up the idea of FFU, and that’s when we decided to give it a try.
- ———Has there been no attempt to replace the natural wood keel blocks with other materials until now?
- Mr. Taguchi : No consideration has been given to anything other than natural wood. The reason for this is, for example, if a ship is docked in a dry dock and placed on keel blocks, and damage is found on the bottom of the ship, it would be very difficult to remove steel or concrete blocks. However, with wooden keel blocks, they can be cut with a chainsaw, removed, and then the damage can be repaired. FFU from Sekisui Chemical can be treated in the same way as natural wood, which is one of the advantages of FFU blocks.
Additionally, with FFU, even if work using flames is being conducted nearby, the risk of fire spreading is minimal. Its flame-retardant properties are also an operational advantage. All told, FFU seems to be the ideal replacement.
- ———I understand that even for steel and concrete keel blocks, natural wood is used in the parts that come into contact with the ship's hull. At Onomichi Shipbuilding, it seems that a set of keel blocks consists of stacking tropical wood blocks, about 1 meter high, on top of the concrete blocks. Is that correct?
- Mr. Taguchi : Modern shipyards create the optimal keel blocks based on their own experience, designed to absorb the weight of the ship and the distortion of the hull. Therefore, even when referring to keel blocks in general, there are various types used at different shipyards. At Onomichi Shipbuilding, we combine concrete and tropical wood for the keel blocks used in the dry docks.
- ———It seems that the FFU keel blocks were used for ship repairs in the dry dock. Are the keel blocks used on the slipway different from those used in the dry dock?
-
Mr. Asami : Our shipyard uses a sliding type for launching, and we use tropical hardwood for the keel blocks and fixed blocks, similar to those used in dry docks. Regarding FFU, we did a small-scale test adoption about 10 years ago, but at that time, since tropical hardwood was still available and FFU was expensive, we decided against it. However, as mentioned earlier, due to the current difficulty in obtaining tropical hardwood, we started using FFU in some of the keel blocks this year. Additionally, we are currently in discussions with Sekisui Chemical to explore the possibility of adopting FFU for fixed blocks in the future. By the way, the FFU purchased about 10 years ago is still in use today.
Keel blocks combined with FFU
- ———So FFU has been used as part of keel blocks for the past 10 years. When did you start considering using FFU for the main structure of keel blocks themselves?
-
Mr. Asami : The actual work began in December of last year, when we conducted suitability tests using FFU.
Suitability tests were conducted on-site in the actual working environment.
- ———As the Dockmaster, I assume you were in charge of overseeing the suitability tests. How did it go?
-
Mr. Taguchi : We had some spare tropical wood keel blocks, but when we brought them here from the local site, they didn’t perform as expected. Exposure to rain and wind caused them to warp, making them unusable. This was one of the reasons for seeking a replacement. However, with FFU, which is also used as railway ties, we were confident that it would not warp or crack, even when used outdoors, making it a valuable alternative as a spare. My concern, however, was that unlike railway loads, ships load a significantly higher weight.
So we first purchased multiple types, and then together with Mr. Nakazawa from Sekisui Chemical, we conducted tests on the shear and bending loads for about two months. We concluded that FFU would not crack under such conditions. Following this, we visited Sekisui Chemical’s factory to begin work on finding the optimal combination of materials for long-lasting keel blocks.A compression test conducted at Sekisui Chemical Industries, Shiga Ritto Factory
- ———Is this the optimal combination of FFU? Could you tell us what that involves?
- Mr. Asami : In the case of natural wood keel blocks, they are stacked in such a way that the ship’s load is applied perpendicular to the direction of the grain. However, with FFU, it is homogeneous, and at the same time, the specific gravity and other properties can be adjusted based on the material composition during manufacturing.
The challenge was to figure out how to combine different configurations of FFU to match the shape and performance of tropical wood keel blocks, while also optimizing for cost performance. We discussed the required performance characteristics for the keel blocks with Sekisui Chemical, who helped create several combination patterns. Through continuous testing and information exchange, we narrowed it down to three patterns.
In July of this year, we purchased 20 sets (bases) of FFU keel blocks. On August 5th, we conducted a trial adoption at the repair site for a RORO ship in No. 5 dry dock.
If these 20 sets work well, we plan to gradually replace the aging tropical wood keel blocks that have cracks with FFU.
- ———How are FFU keel blocks used at the RORO ship repair site?
- Mr. Taguchi : In August, a RORO ship with a deadweight tonnage of 60,000 tons entered No. 5 dry dock, which has capacity for ships up to that size. The ship is approximately 200 meters in length, and out of the 200 center keel blocks, 20 blocks on the stern side were replaced with FFU keel blocks.
The FFU and tropical wood keel blocks are stacked into a set with the same shape, including the wedge blocks for height adjustment, so the work process remains unchanged. However, the FFU blocks are lighter, making them easier to handle.
Additionally, cargo ships tend to have flat, wide hulls to accommodate more cargo, but RORO ships, which require high-speed performance during voyages, have a more tapered hull. As a result, the load from the ship is distributed over only 20 cm of the 40 cm width of each keel block, which is 1.4 meters long. Since the stern side of the ship loads significant weight (this particular ship weighs around 9,000 tons), if this setup works without issues, it will significantly increase the reliability of FFU keel blocks.
However, since keel blocks are used over many years, it will take some time before the tests can be considered fully complete.
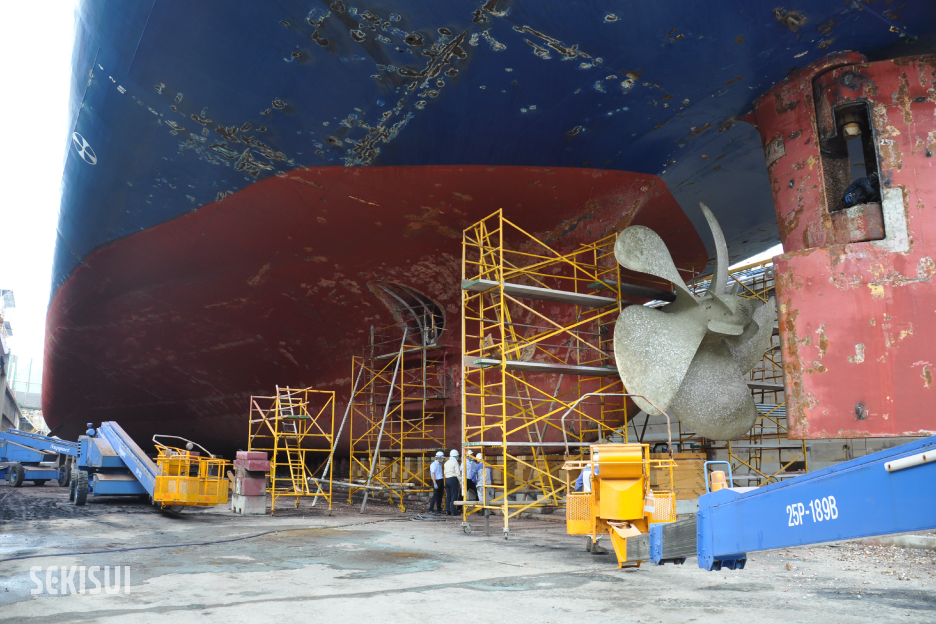
- ———How often are the tropical wood keel blocks that have been used so far replaced with new ones?
- Mr. Asami : I have been with Onomichi Shipbuilding for 25 years, and during this time, we have never significantly replaced the keel blocks inside the dry dock.
Of course, we have replaced keel blocks that have cracked due to aging, or those damaged by factors such as shifting of the blocks or the effects of ship coatings. However, this is the first time we have replaced as many as 20 keel blocks at once.
I believe that while the initial cost of FFU keel blocks may be higher, the running costs are lower, indicating that the value is not just in the price. Let’s continue to collaborate and develop them into something even better.
———Thank you very much.
Natural wood keel blocks, which have supported ships throughout the entire history of shipbuilding, are now facing the issue of resource depletion, evoking a sense of melancholy. However, with Sekisui Chemical's synthetic wood material, FFU, leading the way in keel block innovation, the wisdom of those who have contributed to shipbuilding can be passed on to future generations.
We look forward to continuing our collaboration with Sekisui Chemical's FFU.
Comment from a sales representative
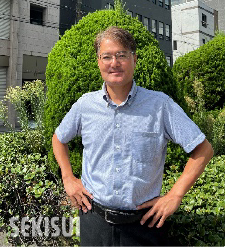
Hideki Nakazawa
Kinki Civil Engineering Systems Sales Office
Western Japan Branch
Dock keels have various demanding quality requirements, including strength, weight, slip resistance, durability, heat resistance, workability, and manufacturability. FFU is considered a material capable of fully demonstrating these qualities.
In deciding on the specifications for this keel blocks, we invited Onomichi Shipbuilding to our Shiga Ritto Plant, where we conducted strength comparisons with the current Apitong (tropical hardwood) material. Onomichi Shipbuilding provided deep insight and many useful ideas for the future, leading to creative specifications, such as altering the fiber direction of the FFU and incorporating our FFU recycled material.
We will continue to collaborate and strive to propose even better specifications to meet their expectations. We hope that FFU will become a leading material for keel renewal in the shipbuilding industry.
Products
The product introduced in this article
Plastic foam material reinforced with long glass fiber
ESLON NEO LUMBER FFU
Product description———
ESLON NEO LUMBER FFU is synthetic lumber made from rigid urethane resin foam reinforced with long glass fibers. It can be used in any field as a replacement material for natural timber. It is at tracting at tention as a mater ial helping to protect the natural environment.
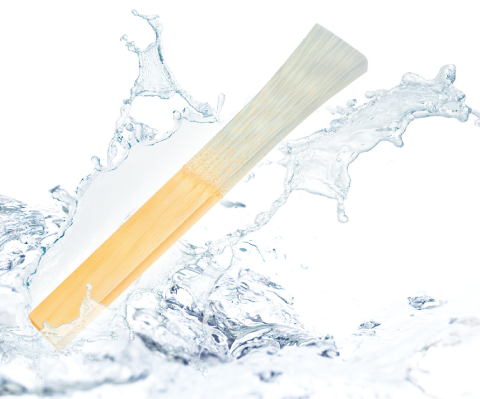
-
1.Like natural material
-
2.Benefits of plastic
-
1.In water treatment plants
As a cover
Excellent durability and enough lightness to foat on water, making it easy to retrieve even after a drop. As the product can be reused over a long term, it contributes to life cycle cost reduction.
-
2.In ports
As floating piers
Excellent water and corrosion resistance, does not require preservative treatment, and does not affect water quality. Environment-aware design is made possible.
-
3.In slopes for disaster prevention
As pressure plates
Excellent workability contributes to the shortening of the construction period and the reduction of costs. In addition, with our fexible and responsiveness design, we are able to propose products matching the site needs.
-
4.In railways
As synthetic sleepers
It has the same quality stability and durability as concrete, but can be constructed like wood, and is used by railway companies.
Comment from a Plant staff member
Katsuhito Takahashi
Functional Materials Technology Department
Shiga Ritto Plant
Our plant is located in Ritto City, Shiga Prefecture, which is near the center of Japan and offers good access both by car and train. FFU has been used for various purposes over the years, but the adoption of FFU in shipyards is rare. When we had the opportunity to visit the dock at Onomichi Shipbuilding, we were overwhelmed by the large scale of the shipbuilding site.
In the compression strength comparison test between FFU and Apitong, Onomichi Shipbuilding visited our Shiga Ritto Plant, where we confirmed that the glass fiber reinforcement effect unique to FFU produced results on par with or exceeding the current materials. We are grateful for this comparative testing with other materials, as it deepens our knowledge.
The shape of the keel blocks differs from the railway ties that we are accustomed to producing, and there are cases where specialized shapes are required. However, we will continue to work on improving manufacturing methods, designing easily mass-producible product shapes (specifications), and ensuring that our customers are satisfied with both the delivery time and quality.